Genomic surveillance through next-generation sequencing (NGS) has become a critical tool in helping countries bolster their emergency and pandemic preparedness tools and protocols. NGS is a high-throughput methodology that enables rapid sequencing of the base pairs in DNA or RNA strain samples. This technique provides an effective, unbiased, and sensitive way to identify virus mutations (new virus strains). NGS can be used in different areas, including helping to track transmissions, studying viral genetics, improving diagnostics, and evaluating the efficacy of control measures.
As countries started scaling up their surveillance efforts since the COVID-19 outbreak, supply chain stakeholders, too, had to hone their expertise to ensure that cost-effective and efficient procurement and distribution mechanisms are in place to support the demand and complexities involved in the procurement and delivery of sequencing platforms, ancillary equipment, and consumables like reagents.
The Partnership for Supply Chain Management (PFSCM) is one such supply chain stakeholder that has, since the start of the COVID-19 pandemic, expanded its product and service offering to help its clients improve their genomic surveillance efforts through access to affordable, quality-assured, compatible and fit-for-purpose NGS products.
PFSCM takes a project management approach to fulfill orders and manage shipments for NGS products. In doing so, PFSCM educates its clients about the requirements and considerations for ordering and taking receipt of these products, helps its clients plan for the long-term success and sustainability of their NGS implementation programs, and helps manage supply chain risks taking pressure off in-country stakeholders and freeing up their time for programmatic health work.
Notable achievements in supply chain management for NGS products:
- PFSCM hosted several educational webinars on the key considerations for the procurement of sequencers and related products.
- PFSCM has a team dedicated to project managing NGS orders, thereby ensuring that common pitfalls are avoided and recipients are empowered to make sound decisions about not only the kinds of products they are acquiring but also about the time frames within which they plan on ordering and receiving the goods.
- PFSCM has, in the first half of 2023 alone, facilitated the procurement of more than $12.8 million worth of NGS products. Please read about our Benin delivery here.
- In 2022, PFSCM floated a tender to negotiate affordable pricing structures for NGS instruments and consumables with suppliers. Through this initiative, suppliers started offering products with discounts, and equity programs were created by several suppliers. These programs ensure fair product prices for eligible countries on an international or regional level.
- By July 2023, at least 12 low- and middle-income countries had NGS orders in the pipeline, demonstrating their commitment to the scale, which is so critically needed in preparation for the next local and/or global health emergency.
Having gained quite a bit of experience in effective supply chain management of NGS equipment, PFSCM compiled a list of some NGS products on offer through PFSCM and summarized some key considerations for procuring and taking receipt of NGS equipment.
NGS products in PFSCM’s portfolio
PFSCM’s approach to strategic sourcing is to build a diverse and reliable supplier base that ensures its clients have access to high-quality products that are affordable and fit for purpose.
Through full and open competitive procedures, PFSCM ensures the timely delivery of quality products and services at a reasonable cost. The organization follows the WHO Model for Quality Assurance (MQAS) for procurement agencies and uses diverse criteria to select suppliers based on “best value.”
With more than 15 suppliers offering specialized NGS products, PFSCM has access to a wide range of quality-assured sequencers, ancillary products, and reagents on offer.
Below are a few examples of the products in PFSCM’s portfolio (view PFSCM’s catalog here).
Sequencing equipment/machines:
On offer through PFSCM is a wide range of sequencers from Agilent Technologies, Illumina, Oxford Nanopore and ThermoFisher Scientific.
From Illumina PFSCM supplies the iSeq100 , MiniSeq, MiSeq, NextSeq 550, NextSeq 1000, NextSeq 2000 and NovaSeq 6000. From Oxford Nanopore the MinION Mk1B Device and GridION MK1 Device, and from ThermoFisher Scientific the Ion GeneStudioTM S5 Prime System, Ion GeneStudioTM S5 Prime System and Ion Torrent Genexus, Integrated Sequencer.
Reagents: Reagents for various workflow steps and elements are available from Agilent Technologies, Illumina, MGI, New England Biolabs, Oxford Nanopore, Roche, Sansure Changsa, Seegene, Shanghai Kehua, ThermoFisher, Vela Diagnostics, and Wantai BioPharm, among others.
Ancillary products: Various products for sample collection and preparation equipment are available from suppliers like BioMerieux, Hain, QInstruments Roche, and Shanghai ZJ Bio-Tech, among others. Library preparation and quality control products are also on offer from suppliers like Agilent Technologies, Applied Biosystems, Biorad, Hain, Hongshi Medical, Qiagen, QInstruments Roche, and ThermoFisher, among others.
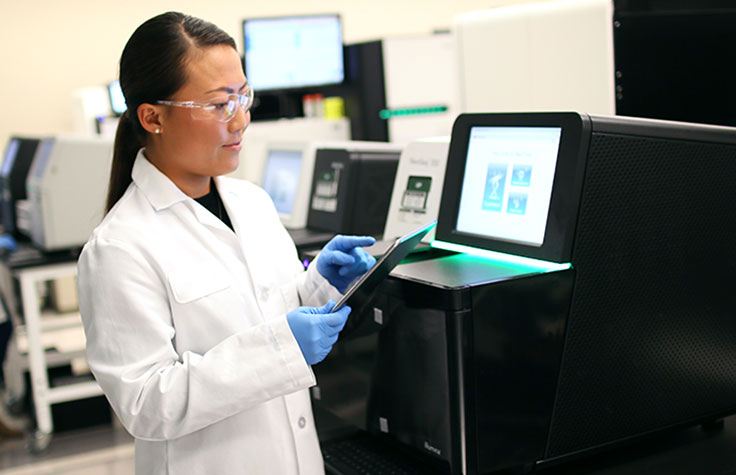
Photos: Illumina. Illumina NGS technology leverages sequencing by synthesis (SBS) technology – tracking the addition of labeled nucleotides as the DNA chain is copied – in a massively parallel fashion.
Key considerations when deciding what NGS equipment to choose
Despite the variety of technologies, methods, workflows, and protocols, there are important factors that clients must consider for a successful NGS implementation; these are:
- The required throughput or amount of samples being processed in a certain amount of time (day/week/month).
- The availability of supplier after-sales services and support in-country.
- The existing infrastructure to comply with installation requirements (space, electricity, etc.).
- The intended use of the equipment (Research Use Only).
- The present and future applications/needs.
- The options for data management and connectivity (storing and sharing data).
Advising clients and managing supply chain risk for successful NGS implementation
For analyzer and sequencer orders, PFSCM works closely with its clients to ensure the requirements for the technology solution are fully understood. Depending on the client’s needs, PFSCM may offer holistic advice on everything from product specifications to maintenance and service agreements, and warranties to training and installation.
PFSCM will consult extensively with the client and may, in collaboration with suppliers, discuss the below issues to ensure that compatible, fir-for-purpose, and sustainable NGS solutions are selected:
NGS research: |
|
Equipment options: |
|
Budget, cost of ownership: |
|
Training and Installation: |
|
Warranties, maintenance, and after-sales service: |
|
Infrastructure and site-readiness: |
|
Supply chain and distribution: |
|
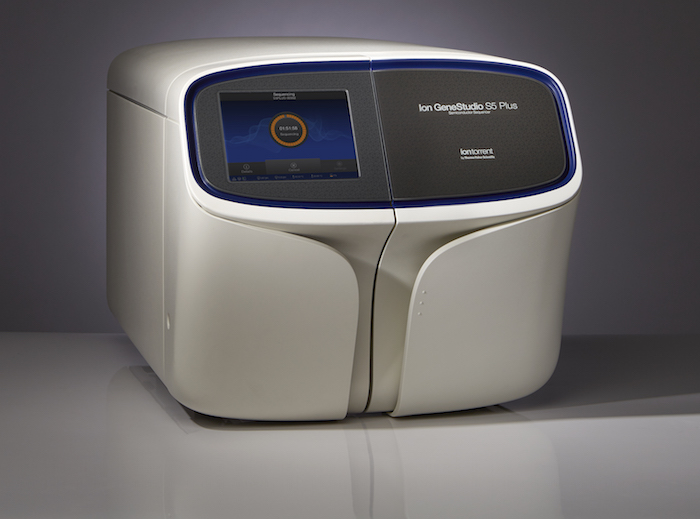
Photo: ThermoFisher Scientific. The Ion GeneStudio S5 System enables scalable, flexible, high-throughput targeted next-generation sequencing (NGS) for a broad range of applications.
Delivering the products and site-readiness
PFSCM also supports its clients with logistics solutions, and works closely with suppliers to ensure that products, specifically NGS goods, are delivered to the various destinations in a cost-effective and timely manner.
For NGS goods, PFSCM worksl closely with suppliers and clients to determine what the best Incoterms for delivery will be. PFSCM may assist clients with project-management activities to help them ensure site readiness. If the site for the placement of the NGS products is not ready, then goods cannot be delivered, and the implications for the upstream supply chain and health program can be severe.
Site readiness depends on sector and project type, and may range from simple activities, such as ensuring that there is enough room in the laboratory for the machines, to more complex issues, such as appropriate electrical supply. Each sequencing machine will come with its own list of site preparation specifications, and generally, the client (buyer) is responsible for ensuring site readiness before equipment can be commissioned and installed.
PFSCM, along with donors, and suppliers, offers clients support in achieving site readiness and may travel to installation sites to help determine if and when sites are to take receipt of products.
Installation, training, and start-up and commissioning services (if included in PFSCM’s offer), can only be scheduled from two to four weeks after the device has been delivered and once the site is ready. PFSCM may require a client (or end-user) to commit to having the site ready for installation or training no later than the scheduled estimated delivery date.
Examples of site preparation guides by suppliers:
- Agilent 4200/4150 TapeStation – Site Preparation Checklist
- MiSeq System – Site Prep Guide
- ABI 3500/3500xL Genetic Analyzer
Transport planning for short shelf life reagents
In the pharmaceutical molecular biology industry, the shelf life of a product is crucial. Many pharmaceutical molecular biology products are temperature sensitive and have a short shelf life, which requires them to be refrigerated or kept in controlled environments for only specified periods of time. This presents challenges for inventory management and supply chain, leading to the possibility of product wastage. The average shelf life of many NGS reagents is three months, but it may vary according to the requested product(s).
To help manage the risk associated with shipping short-shelf life reagents from abroad, PFSCM helps its clients with various transport planning solutions:
- PFSCM collaborates with clients and supply chain stakeholders to expedite the import and tax/registration waiver lead times if possible.
- PFSCM determines the most suitable Incoterms and often arranges air shipments to accommodate temperature-controlled and cold chain products.
- PFSCM monitors the number of reagents that are being requested by clients. If the amount seems high for the given throughput of a machine in the specified time span, PFSCM works with the supplier to arrange staggered deliveries.
Staggered deliveries refer to the practice of delivering goods in batches or at different times rather than as a single shipment. This method is widely used by organizations to manage their inventory levels, reduce warehousing costs and improve customer service. Staggered deliveries can be implemented in several ways, depending on factors such as the type of product, storage capacity, and customer demand. This helps to manage inventory and reduce wastage that may occur.
Staggered deliveries are usually more expensive as compared to bulk deliveries, and it requires more precise planning and coordination between the manufacturer and the distributor.
Below is an example of how deliveries could be staggered to preserve the shelf life of the reagents:
- Batch one: device is shipped.
- Batch two: a month later, the device has arrived, and services are scheduled.
- Batch three: a month afterward, the services are carried out, and we program the first delivery of reagents.
- Batch four: the rest of the reagents, delivery according to the agreed time interval.
Staggered deliveries can provide several advantages:
Improved inventory management: | Staggering deliveries helps to keep inventory levels low, reducing the need for costly warehousing space. |
Reduced warehousing costs: | By reducing the frequency of deliveries, organizations can save on warehousing and storage costs. |
Better customer service: | Delivering products in smaller batches provides more flexibility in meeting customer demand and can result in faster and more reliable deliveries. |
Reduced risk of stockouts: | By staggering deliveries, organizations can better manage their stock levels, reducing the risk of running out of stock. |
To effectively implement staggered deliveries, organizations need to follow several steps:
- Analyze customer demand: it is essential to understand how often clients order products so that the organization can schedule deliveries accordingly.
- Strategize the delivery frequency: organizations should determine the optimal delivery frequency so that they can manage inventory levels without incurring excessive shipping costs.
- Plan for storage and handling: organizations need to ensure they have adequate storage space and equipment to manage staggered deliveries. They may also need to modify existing warehouse layouts to maximize storage space.
- Adjust supply chain planning: staggered deliveries can require significant changes to the supply chain, so it’s important to establish strong communication with suppliers to coordinate deliveries effectively.
- Monitor results: organizations need to track performance closely, measuring inventory levels, customer satisfaction, and transportation costs to ensure that the staggered delivery system is working optimally.
Staggered deliveries can provide significant benefits to organizations looking to manage their inventory levels, reduce warehousing costs, and enhance customer service. By following the key steps outlined in this blog, and taking into account important considerations, organizations can implement staggered deliveries effectively and gain a strategic advantage in the marketplace.
Learn more about NGS and NGS workflows
What is genomic sequencing using NGS?
NGS and specific NGS workflows