by Sinette Goosen, PFSCM Communications Officer based in the Netherlands.
The Partnership for Supply Chain Management (PFSCM) has recently strengthened its cold chain capabilities, not only to meet and exceed the changing needs of our clients, but also to prepare for the current, and imminent increased demand for cold chain shipping that is both driven by COVID-19 vaccine distribution, and at the same time hampered by ongoing pandemic restrictions and lockdowns.
PFSCM has always been involved in the transportation of time- and temperature-sensitive products (TTSP) for various clients, but it was really in 2019 that we ramped up our expertise in this area, and started partnering with specialist providers who add real value to our service offering.
In 2020, our efforts to entrench ourselves with as much cold chain knowledge as possible started coming to fruition, and we successfully delivered more than 500 cold chain shipments to challenging low- and middle-income countries (LMICs). In 2021, we continued to build on this strong foundation by partnering with insurtech company Parsyl to deploy temperature data loggers in all our cold chain shipments.
Our cold chain journey since 2019 has included adapting processes and systems, creating policies and guidelines, engaging suppliers and service providers, developing tools, and researching and implementing best practices for sustainable shipping of lifesaving TTSPs such as the viral load diagnostics, early infant diagnostics, rapid diagnostic tests, and other laboratory and diagnostic products for the detection, prevention and treatment of COVID-19, HIV, malaria, and tuberculosis among other diseases.
We were able to embark on this journey because we have reliable business models and approaches in place. The key driver for our adaptability is our 4PL model which gives us data visibility, and enables us to select best in-class service providers, and change 3PLs as necessary to control costs. Our 4PL model paired with our Control Tower also equips us to monitor the performance of a wide selection of partners.
Another discipline that helped us structure our cold chain approach is our ISO 9001:2015 certified Quality Management System, which guides us in either creating new processes, or adapting existing ones; and forces us to use data to evaluate the efficacy of our work so that continuous improvement can be achieved.
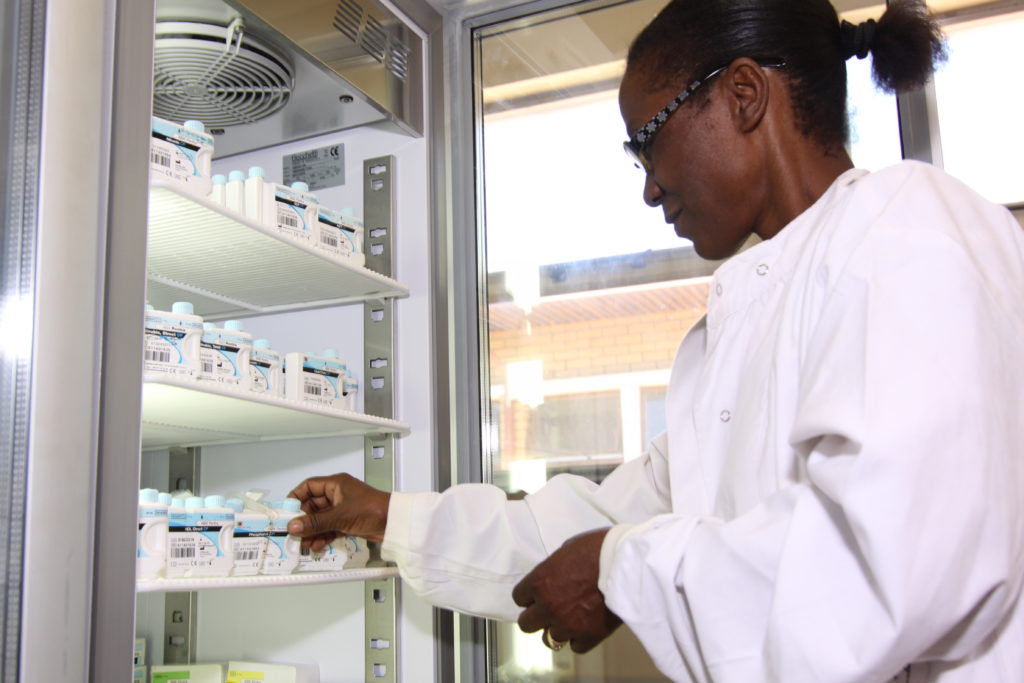
More than 90% of PFSCM’s volumes are destined for countries in Africa where, owing to a variety of reasons, the delivery of health products is especially complex, and even more so for TTSP.
Activities and innovations to strengthen cold chain management
Specialized 3PLs:
PFSCM has an excellent track record of working with world-class 3PLs.
Historically, the majority of PFSCM’s shipments did not require cold chain or temperature control, and thus the partners we collaborated with did not specialize in these fields.
In 2019, we started researching specialized cold chain 3PLs, and partnered with organizations that have experience in serving the health logistics, and humanitarian aid sectors; and also understand the challenges and requirements of shipping to LMICs; some of which face very real challenges such as a lack of resources, and basic infrastructure.
More than 90% of PFSCM’s volumes are destined for countries in Africa where, owing to a variety of reasons, the delivery of health products is especially complex, and even more so for TTSP.
Two of our new notable 3PL partners include Logenix International and Cyberfreight headquartered in the US and the Netherlands, respectively.
Logenix International has become recognized for serving global health programs, disaster relief-, infrastructure and development projects, security and contingency operations, as well as other high profile projects in the world’s most challenging regions.
Cyberfreight specializes in pharma logistics. They are licensed custom brokers that have their own bonded warehouse at Schiphol Airport where they arrange everything from packing-repacking and labelling to the import and export of shipments. From their office located near the Rotterdam Port, they carry out all ocean freight services including distribution and warehousing.
People:
PFSCM’s logistics staff are qualified professionals with many years of experience in managing supply chains in the public and private sector. Many staff members have previously worked for 3PLs and bring with them extensive freight forwarding experience that makes them uniquely qualified to drive continuous improvement initiatives from an informed perspective.
Processes:
By leveraging our years of niche logistics experience, and by proactively engaging with 3PLs and suppliers, we have developed agile logistics processes that enable us to adapt to the ever-changing global health environment. This may entail flexibility in freight forwarder selection, route or lane allocation, warehousing and storage location, and packaging and re-packaging activities.
Through close collaboration with our clients, and their recipients, we developed processes for shipping TTSPs, mapped complex importation processes, and secured waivers in many countries.
In 2020, we had great success in remapping the Tanzania importation process. This complex process is still evolving, and being refined by various supply chain stakeholders.
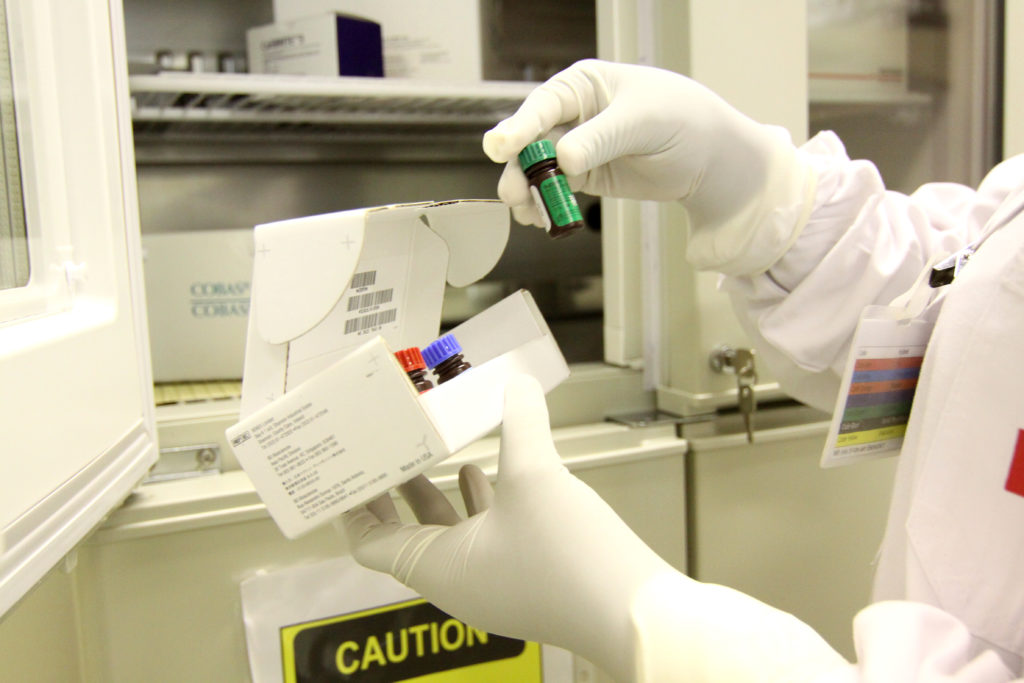
PFSCM ships lifesaving TTSPs such as the viral load diagnostics, early infant diagnostics, rapid diagnostic tests, and other laboratory and diagnostic products for the detection, prevention and treatment of COVID-19, HIV, malaria, and tuberculosis among other diseases
Systems:
We use our One Network Control Tower to collect, and analyze valuable logistics data to improve supply chain visibility.
The Control Tower provides near real-time, track-and-trace shipment information, and also orchestrates other processes such as freight quotation and transport document management to ensure quicker turnaround times.
By connecting our clients, and vendors to this single digital cloud platform, we are collaborating faster and smarter; ensuring the cost-effective, and timely delivery of lifesaving health products.
Temperature data loggers:
In 2020, we partnered with insurtech company Parsyl to deploy data loggers in all our cold chain and temperature controlled shipments.
Data loggers, or sensing devices monitor and capture valuable information about the temperature and humidity commodities are exposed to during transportation and storage. This information can be used to better understand shipping conditions, and more effectively manage risk should any irregularities occur.
Data captured by these devices also play a critical role in increasing accountability among stakeholders, planning for future shipments, reducing waste, ensuring product integrity is maintained during shipping, and improving the overall efficiency of insurance claims.
Tools:
PFSCM uses innovative tools such as automated rate schedules, and load optimization to speed up freight quotation lead times, increase cost predictability, reduce waste, and ultimately, save costs.
Our load optimization tool is an automated calculator that uses vendor and 3PL data to determine the optimal loading formation for various quantities, and types of products being shipped by various modes of transport.
This tool has been exceedingly successful in saving costs and reducing waste.
Recently, for COVID-19 diagnostics we have been able to save about $1 million by just changing the type of pallet used for transportation. Owing to the complexity, and vast amount of information produced by a single transaction, such a simple modification is not easy to identify without the use of an automated tool.
Ultimately, we have been able to advise shippers on how to best load pallets and containers, and have even been able to demonstrate the value of changing packaging sizes for optimal space use.
Policies and guidance:
As an ISO 9001:2015 certified organization, PFSCM uses quality audits, and self-inspections to evaluate its policies, processes, and procedures ensuring they are updated, retired or improved as needed. These activities may also reveal if new policies are needed.
In 2020, PFSCM developed a new policy on the use of temperature data loggers, and also created robust guidance on the transportation of TTSPs.
PFSCM’s policy on the use of temperature data loggers provides an overarching framework to all processes related to shipment planning and management until delivery of goods to final consignee.
Our guidance on the transportation of TTSPs sets out key requirements for transportation of these products, and is used for shipment planning. This includes all pharmaceuticals, vaccines, biologicals, in-vitro diagnostics, and medical devices, which, when not stored or transported within predefined environmental conditions and/or within predefined time limits, are degraded to the extent that they no longer perform as originally intended.
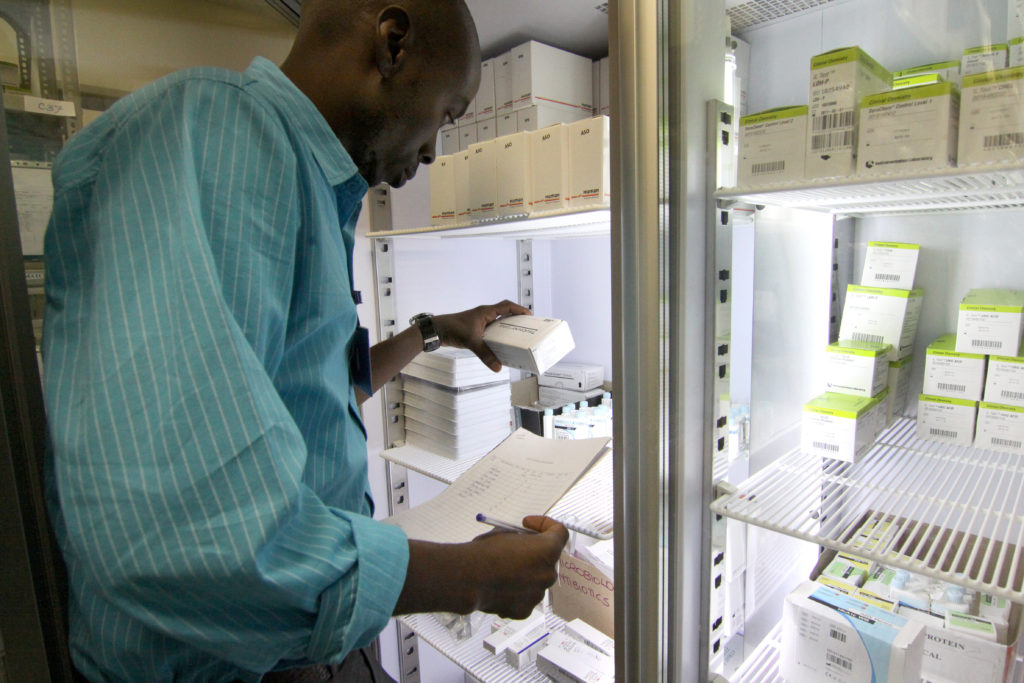
When TTSPs are not stored or transported within predefined environmental conditions and/or within predefined time limits, are degraded to the extent that they no longer perform as originally intended
Insurance:
PFSCM is also making use of Parsyl’s cargo insurance offering through the Global Health Risk Facility (GHRF), a public-private syndicate formed by an alliance of insurance and technology partners to strengthen supply chains and prepare countries for the distribution of Covid-19 vaccines and other critical diagnostics, treatments and supplies.
In January 2021, PFSCM became the first GHRF policy holder. This demonstrates PFSCM’s agility in seizing opportunities to partner with dynamic organizations that share our mission of delivering high-quality health products to underserved populations.
Through Parsyl’s GHRF we have access to technology, data, cargo insurance and risk management services that support end-to-end visibility, and data-driven decision making for improved supply chain management.
Supplier engagement:
Supplier engagement is of utmost importance to PFSCM. COVID-19 has revealed how invaluable good vendor relations are to any business. We have always strived to meet with our 3PLs regularly, but since the pandemic we have increased the frequency with which we engage our freight forwarders, and we have also devised better structures for communicating the correct kind of information at the right level. It is mutually beneficial that the organizations understand each other’s operations to collaborate more effectively.
PFSCM’s logistics team will soon start hosting vendor workshops to:
- Educate our 3PLs to help us achieve better KPIs.
- Eliminate issues resulting from lack of information.
- Build stronger business relationships based on transparency, trust and familiarity.
- Facilitate knowledge exchange sessions to learn from each other.
- Support continuous improvement.
Sustainability and best practices:
Ethical, sustainable practices are at the core of our daily operations. Our business decisions indirectly affect the outcomes of global health programs, and ultimately play a role in saving people’s lives, and improving health outcomes for millions of patients.
For PFSCM, corporate sustainability through responsible business activities, is an inexpugnable company culture.
To support and formalize our approach to sustainability and best practices, we have adopted many of the principles for sustainable business as set out in the UN Global Compact’s 10 Principles.
Action and innovations that drive sustainability and resilience:
- Consolidation of cargo for cost-savings, a reduced carbon footprint and simplified transport management.
- Using appropriate technologies such as sensing devices and Control Towers to capture supply chain data enabling better decision making for improved resilience.
- Load optimization to ensure pallets and containers are used optimally.
- Cross-collaborating with peers to co-load shipments for optimal space utilization, and cost savings.
- Partnering with organizations who share our mission to reduce the logistics carbon footprint and drive supply chain resilience.
- Carrier neutral 4PL approach that allows us to select the best freight forwarder for the job based on cost, performance, sustainability and experience.
- Selecting suitable modes of transportation that prove cost effective, safe and sustainable.
- Developing in-county logistics and last-mile delivery systems to uplift small businesses, and stimulate local economies.
- Planning for reverse logistics and waste management to reduce the burden on developing countries.
- Support distribution and packaging innovations such as cartonless packaging and the delivery of multi-month prescriptions.
- Advise countries on best practices for order cycles which may either be smaller shipments more frequently, or larger shipments less often.
Last word
PFSCM has shown agility and resilience in responding to the cold chain and COVID-19 challenges currently faced by the health- and humanitarian logistics sector.
By becoming true cold chain experts, we will not only be able to better deliver medical devices used in the prevention, detection and treatment of HIV, TB and malaria, but we will also help intensify the fight against the COVID-19 pandemic through the delivery of diagnostics and vaccines.