The Partnership for Supply Chain Management (PFSCM) has been a Procurement Services Agent (PSA) and health and humanitarian logistics services provider for over 15 years and has constantly evolved and reinvented itself to meet the rigors of public health supply chains.
PFSCM serves donors, NGOs, governments, ministries of health, and humanitarian aid and relief agencies. The majority of PFSCM’s work entails strategic sourcing, transactional health procurement, quality assurance and logistics for the public sector.
Since 2019, PFSCM served clients in 105 countries, transacted more than $1.26 billion worth of orders for medical devices, and delivered more than 5,600 shipments.
One of PFSCM’s core services and capabilities is health and humanitarian logistics. PFSCM works closely with a network of reliable freight forwarders to ensure products are delivered on time and in full to some of the most challenging destinations on earth.
In the health and humanitarian logistics space, the allocation and management of shipments is a unique and often complicated task varying from high volume and fairly standard, to low-volume and quite complex shipments. Already intricate logistics tasks are further complicated by ever changing social, political and economic conditions in many of the low- and middle-income (LMICs) countries served.
PFSCM 4PL Director Ishmael Muchemenyi explains that the recent severe freight market turbulences such as total airspace closures, continuing lockdowns, reefer container and labor shortages, and soaring freight costs — that were once considered “real exceptions” have now become the “new normal” operating climate for logistics service providers.
Muchemenyi adds that PFSCM is adept at managing tough logistics conditions, but has had to “evolve” even further to keep up with the fast-changing and unpredictable freight and supply chain conditions.
“We are accustomed to rapidly changing logistics situations, but in the last three years; first with the outbreak of COVID-19, and then more recently with the conflict in the Ukraine, we have had to transform our management and partnership approach for logistics almost entirely.”
Muchemenyi explains that PFSCM adjusted its overall strategy to build greater resilience in our shipment execution as the wider supply chain market continues to move away from the just-in-time model to the just-in-case model.
“We recognize that complexity demands control, and by evolving our strategy we can overcome adversity through planning for the unexpected. This also means transforming into an all weather type of service provider that can thrive in both normal and abnormal conditions.”
He concludes that the recent supply chain disruptions have taught supply chain professionals to expand their service options and to think and act outside the box. To do this effectively, it is no longer sufficient to simply outsource the distribution function to 3PL organizations but to do so in a smart and informed manner, allowing greater end to end visibility and even the ability to propose alternative solutions.
We spoke to a few of PFSCM’s Logistics Specialists to learn more about situations in which PFSCM was able to leverage partnerships and demonstrate its logistics and supply chain expertise to overcome unique challenges.
Unique health and humanitarian logistics responses
Yemen – ensuring service continuity despite ongoing conflict
PFSCM has been serving Yemen since before the Civil War started in March 2015. In fact in the last six years (2016 to 2021) PFSCM has delivered more than $3 million in goods through 82 shipments, despite severe limitations on transport options to the country.
PFSCM’s service offering to Yemen comprises procurement and logistics services for three major Principal Recipients (PRs), which are all headquartered in Sanaa and receive millions of dollars worth of health commodities annually.
Shipments for Yemen have comprised a mix of more than 70 different types of products including rapid diagnostic test for malaria, HIV and COVID-19, antiretrovirals (ARVs), antimalarials, viral load and early infant diagnostic analyzers, laboratory equipment and consumables, and reagents to name a few.
PFSCM Logistics Lead Elena Feldsherova explains that when the war broke out in 2015, global 3PLs were suddenly grounded, all ports were taken over by the military, and all shipments were diverted to Djibouti causing major port congestion and a chaotic situation.
“Back then, PFSCM experienced major service delivery disruptions including shipment delays, damages, losses, switched and missing documents,” she adds.
Feldsherova says PFSCM had to act quickly to find solutions to the dire logistics situation.
“Using the flexibility of our 4PL model, we immediately onboarded the World Food Program (WFP) who in collaboration with the UN Logistics Cluster, is one of the only organizations delivering aid and goods into Yemen.
“Initially, it took some time for PFSCM and WFP to understand what processes will ensure the success of the working relationship, but close collaboration to align processes has resulted in simple but smart improvements.”
She explains that one such improvement is the consolidation of shipments to have multiple shipments from multiple origins (with similar Client Incoterms) scheduled to arrive at a main port or airport whether in Yemen or a neighboring country simultaneously. These shipments are then consolidated into one large shipment, thereby reducing the risk of smaller shipments being lost, and speeding up the customs clearance process, she adds.
Further, Feldsherova says even though service levels are not as high as under normal circumstances (and this can be expected of conflict countries), with the assistance of the WFP, PFSCM has been able to successfully deliver all its scheduled shipments to Yemen, and will continue to do so.
“The WFP has certainly become a trusted and strategic partner, and PFSCM is grateful for their service.”
The WFP was contracted for shipments to Burundi in 2015 and 2016 and still delivers PFSCM shipments to Syria and Yemen.
“When PFSCM started working with WFP for deliveries into conflict countries several years ago, we relied especially on their charter and air cargo options. This was because many of the laboratory and pharmaceutical products that PFSCM was shipping at the time, were time and temperature sensitive,” adds Feldsherova.
More recently, despite limited cargo space availability and a shortage of reefer containers, PFSCM has also been able to benefit from ocean cargo options.
In 2021, PFSCM shipped more than 36,000 malaria rapid diagnostic test (MRDTs) kits to Yemen via ocean freight. Each test contains 25 tests and the shipments amounted to 23 standard pallets. The temperature controlled orders comprised two shipments which were consolidated in two reefer containers in South Korea, before being transported further to Hodeidah Port.
In conclusion Feldsherova says PFSCM has already received orders for 2022, and remains committed to working with its trusted partners to ensure lifesaving testing, prevention and treatment products reach those in need.
Pakistan – overcoming trade restrictions, production delays and reefer shortages
PFSCM has been serving Pakistan since 2010 on an ongoing basis. In 2019, and again in 2021 and 2022 PFSCM had opportunities to assist the country with emergency orders for HIV and malaria testing and treatment products.
In the last six months, despite Pakistan’s trade restrictions on imports from India, production delays and reefer container shortages, PFSCM has been able to assist the Directorate of Malaria Control (DOMC) in the country with large and urgent deliveries of MRDTs. Between December 2021 and June 2022, PFSCM has delivered more than 8.5 million MRDT kits to Pakistan; with more deliveries in the immediate pipeline.
The recent shipments consisted of 14 reefer containers, amounting to 95 metric tons, which were delivered by ocean and another 11 tons of MRDTs delivered as air cargo, bringing the total to 106 metric tons.
PFSCM Logistics Specialist Tassos Betzelos explains that expediting the procurement and shipping required extensive coordination with suppliers and 3PLs.
“Urgent orders require all hands on deck to advocate for shorter production and documentation approval lead times, as well as speedy delivery using the first and most suitable available freight options in order to prevent possible stockout situations for our clients”
He adds that with many years of experience in this regard, PFSCM is well-positioned to negotiate and collaborate with suppliers and shippers.
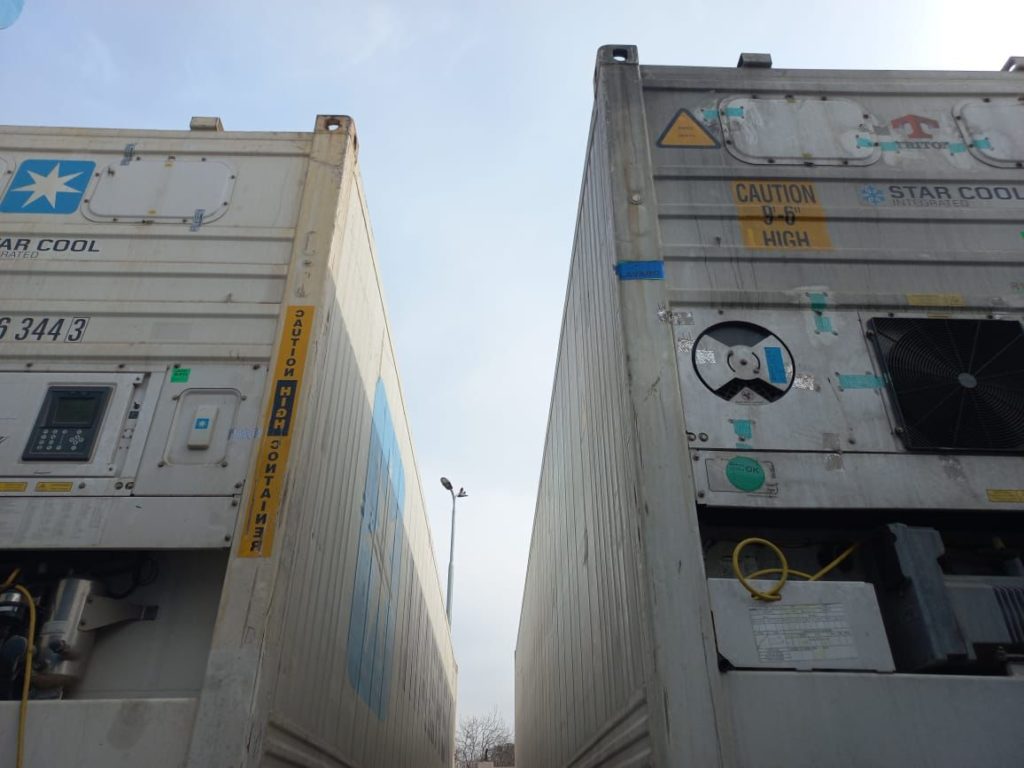
Photo 1: Reefer containers, or refrigerated containers, are used for goods that need to be temperature controlled like the malaria rapid diagnostic test kits that were shipped to Pakistan. Here the reefer containers with MRDTs can be seen at the end destination, Pakistan. Credit – Meril
“COVID-19 is still affecting supply chains, and when we worked on these orders last year we and our stakeholders were still experiencing the knock-on effects of the pandemic. Despite those ongoing global issues, we worked closely with our supplier to prioritize production. The supplier was able to reduce the lead time for the first urgent MRDT order to about 50 days. This is a 25 to 40 day improvement on the standard 75 to 90 days lead time usually offered.
Further, PFSCM collaborated closely with its 3PL partner Maersk to overcome some unique logistical barriers that were presented during planning of ocean shipments.
“At the moment urgent deliveries to Pakistan are not only complicated by the trade restriction imposed on imports from India, but also by the global shortage of reefer containers.”
Betzelos notes that PFSCM recognized these issues in the early stages of supply chain planning, and prior to procurement and shipping, engaged all the stakeholders — Maersk, their legal team, the supplier, the donor, the PR and the Pakistani authorities — to ensure that all the necessary exemptions were in place, and that import waivers were pre-approved for accelerated delivery.
He explains that the exceptions are based on an Import Policy Order from 2016 (and a clause added in 2019) stating that “therapeutic products regulated by the Drug Regulatory Authority of Pakistan (DRAP)” are exempt from the trade restrictions.
“We are extremely pleased and grateful that the supplier and 3PL were able to accommodate these urgent orders despite ongoing supply chain challenges. The dedication and flexibility of our suppliers and 3PLs are testament to our collective commitment to end serious epidemics like malaria, HIV and tuberculosis,” concludes Betzelos.
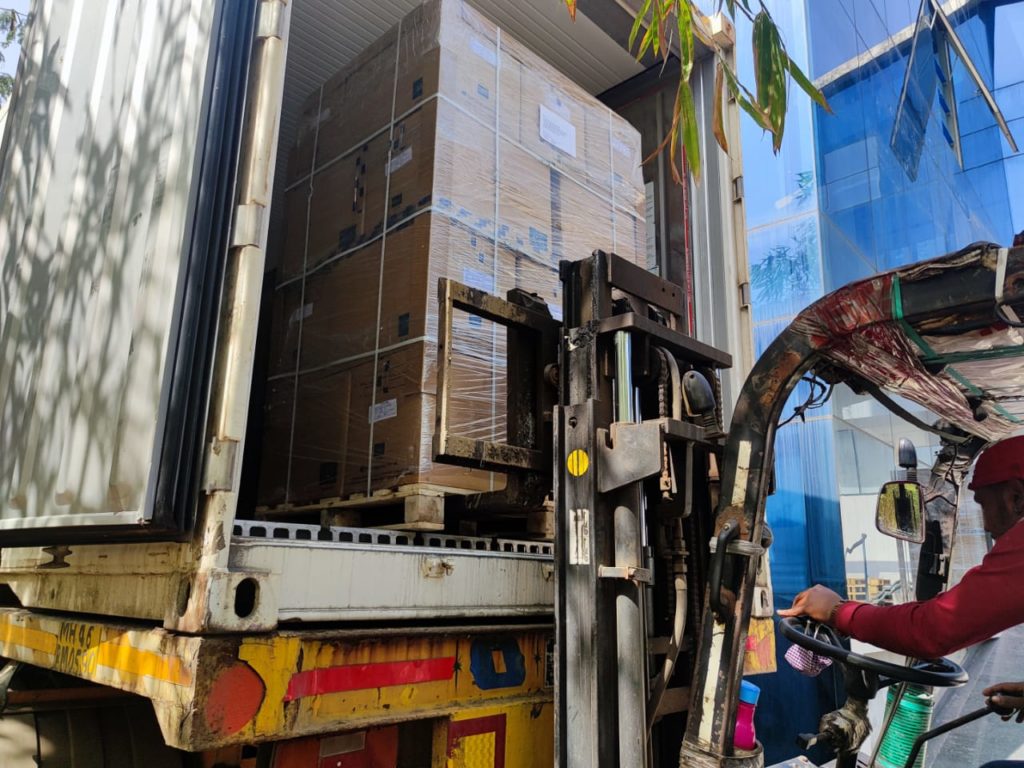
Photo 2: Despite trade restrictions, production delays and reefer container shortages, PFSCM has delivered 8.5 million malaria rapid diagnostic test kits to Pakistan since December 2021. Credit – Meril
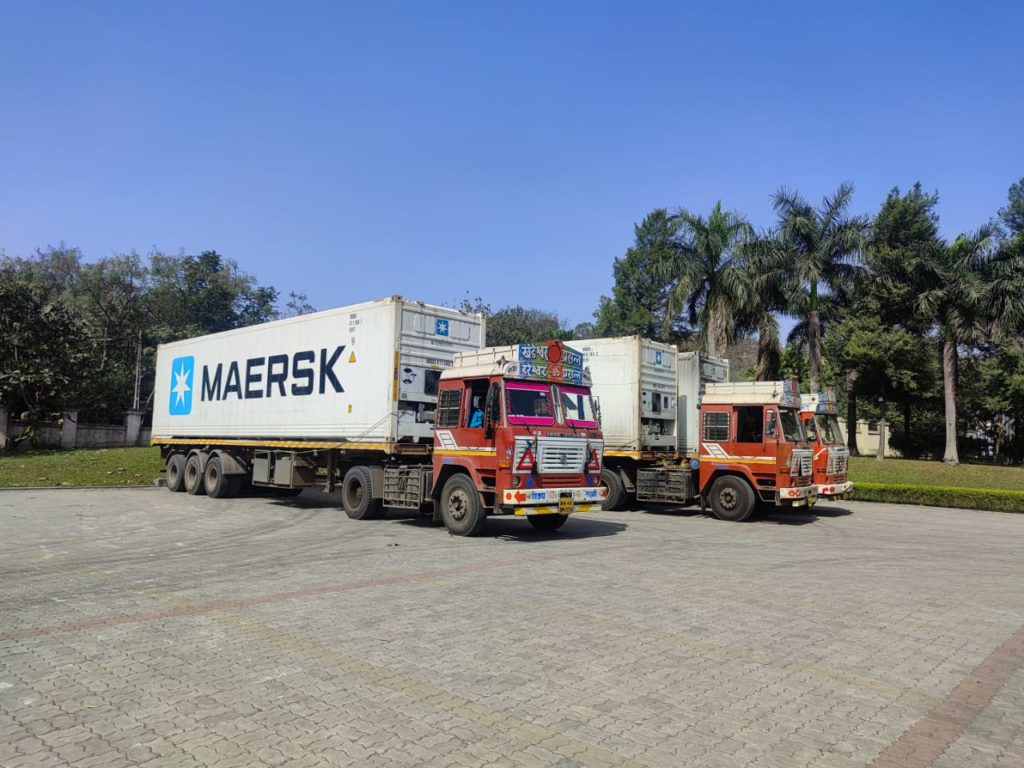
Photo 3: Stakeholders — Maersk, their legal team, the supplier, the donor, the principal recipient and the Pakistani authorities — all collaborated in the early procurement and shipment planning stages to ensure that all the necessary exemptions were in place, and that import waivers were pre-approved for accelerated delivery. Credit – Meril
Meanwhile, back in 2019, when over 900 children were diagnosed with HIV in a pediatric outbreak of the virus due to negligence in reusing needles and syringes, PFSCM quickly delivered 18 shipments of pediatric antiretrovirals (ARVs) and HIV rapid diagnostic test kits, worth more than $200,000 to the country.
PFSCM’s procurement unit worked closely with various suppliers to determine- and release available stock, and plan for the immediate replenishment to supply the new and ongoing orders to Pakistan. PFSCM also collaborated with the donor and PR to clear the waivers as soon as possible.
Overall, PFSCM’s freight estimation and purchase order was prepared in only two hours and the supply- and waiver lead time was reduced by 7 to 10 days.
No stockouts occurred and there were enough commodities to “test-and-treat” during this unfortunate outbreak in 2019.
Nigeria – navigating abrupt changes
Nigeria has always been a challenging destination for health products and humanitarian aid deliveries. The country’s unique and complex business culture, paired with infrastructure, environmental and socio-economic issues, makes it a very demanding destination in terms of supply chain management.
PFSCM has been managing transactional health product procurement and logistics for Nigeria since its inception in 2005. PFSCM first served Nigeria under the Supply Chain Management System and then continued to support the country to this day.
Since 2016, PFSCM procured more than $256 million worth of health products for Nigeria and delivered more than 770 shipments. Nigeria is one of PFSCM’s top countries based on value and volume of goods procured and delivered annually. PFSCM has a dedicated staff member residing in Nigeria to support engagement with the PRs, suppliers, 3PLs, clearing agents and customs- and port authorities.
PFSCM has always gone the extra-mile with shipments for Nigeria ensuring it overcomes the many hurdles as effectively as possible.
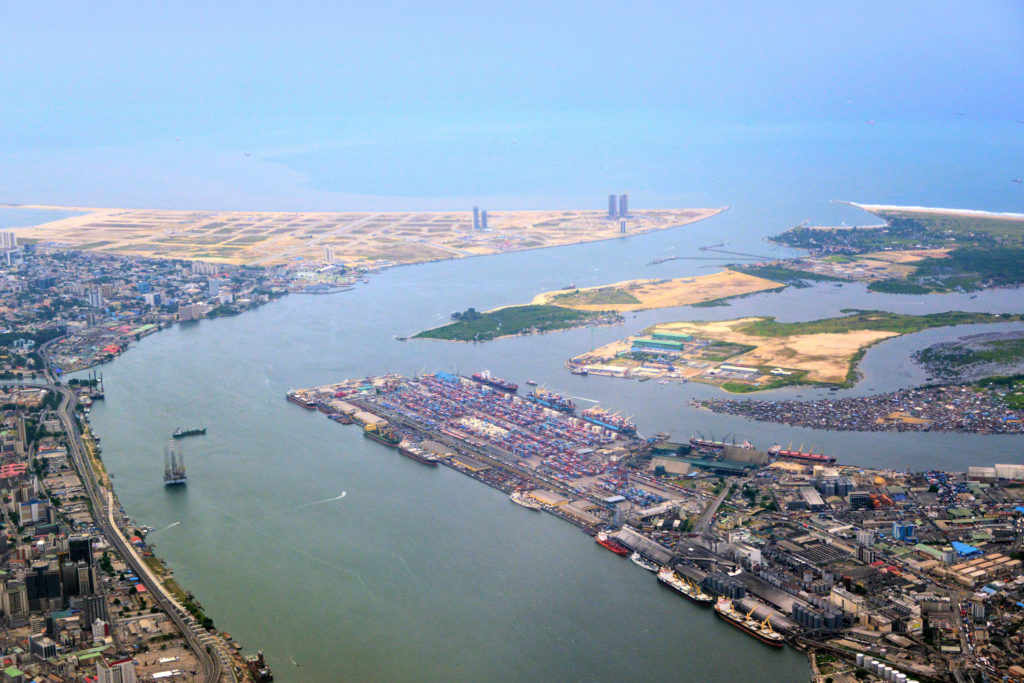
Lagos, Nigeria: the city from the air – Lagos island business district, Victoria Island and Port of Lagos (Apapa Port, container terminal).
Over the years PFSCM encountered many unique shipping and importation situations in Nigeria. From the apparent superfluous completion of the e-Form M around 2017, which in on its own accounted for about eight weeks of the importation process, and road congestion and infrastructure issues at the port of Apapa in 2018, which resulted in trucks queuing for weeks to collect containers, to industrial strikes and political unrest in 2019, and of course severe logistics disruptions as a result of COVID-19 since 2020.
On top of that, in 2020, Nigeria also implemented an automated online import duty exemption certification (IDEC) system to replace the manual process; an initiative for the good that first had to go through some teething pains.
The Nigerian government reported that the decision to automate the process was part of the its effort to eliminate human interface in the processing of duty waiver applications.
PFSCM Logistics Lead Fillip Dias explains that PFSCM welcomed the process change, but like with any system change, PFSCM and other stakeholders had to work through some of the initial teething problems.
“The automated IDEC process is great for improved visibility and significantly speeds up the waiver approval process. Initially, as recipients and other stakeholders started using the system we encountered some expected barriers, but now a couple of years into the process we are starting to see the benefits. Overall, the processing time for granting duty waivers has been reduced to an average of three and five working days.”
Dias further explains that while PFSCM was coming to grips with the new IDEC process, it tightened controls on its side to ensure that all the documents required to ship products to Nigeria were in order and double checked.
“As an extra risk prevention measure we established a cloud repository and checklist to collect and keep track of all importation and shipping documents while the principal recipients came to grips with managing the whole waiver approval process in the automated IDEC system.”
Dias adds that the new repository and checklist proved to be extremely useful and was adopted as a standard practice within PFSCM not just for Nigeria, but for other countries too.
In conclusion, Dias notes that PFSCM has taken a very hands-on approach in managing logistics and transport to and from Nigeria. “We have a dedicated PFSCM representative in Nigeria to assist stakeholders co-ordinate inbound shipments and required documentation in person, we also engage the principal recipients proactively and continuously monitor supply chain developments and plan for known and unknown scenarios as far as possible. We also collaborate closely with the donor to ensure optimal supply chain efficiency, and we are very grateful for this joint effort.”
Tanzania: encouraging stakeholder engagement when change is the only constant
PFSCM has been serving Tanzania since it set up shop. PFSCM manages the procurement and delivery of health care products purchased by the country through a number of grants. Tanzania is one of PFSCM’s top five countries for volume and value of procured products.
PFSCM has a deep understanding of the requirements for serving this country, and service performance has always been high.
In 2019, service was disrupted when the country abruptly changed the requirements for cargo clearing. The sudden changes resulted in a complex network of problems in clearing and forwarding healthcare goods at Tanzanian ports. Several service providers’ goods were suddenly stranded, and detention and demurrage (D&D) costs quickly mounted, while health programs were placed at risk. The abrupt changes affected several of PFSCM’s shipments, and resulted in a decline in service performance.
PFSCM was not the only organization affected by the changes; other companies serving HIV, malaria, tuberculosis, and vaccines programs in the country were experiencing the same issues, and have all been involved in trying to find solutions, explains PFSCM Senior 4PL Services Officer, Andy Savoy-Burke.
PFSCM has encountered unusual, and abrupt process and legislation changes in the past, and had the right knowledge and tools to investigate the situation and find solutions.
“We have importation process maps in place for all the countries we serve. Some years ago, we experienced the same kind of challenges in Nigeria and Sierra Leone, and developed a template for mapping importation processes. The foundation of this template remains relevant today, and we learned from these lessons to build a strategy for remapping the Tanzania importation process,” explains Savoy-Burke.
PFSCM engaged with involved parties such as 3PLs, clearing agents, the ports authority and government entities involved in the process to understand their current capabilities, processes, staff complement, challenges and backlogs. PFSCM then collected and deciphered the feedback to determine how responsibilities have shifted, where gaps in accountability are, and which processes are overlapping or missing.
“We then used the vetted information to create a new importation process overview. The idea was to map out not only the flow of products, but also the timing of payments, documentation submission, and timely confirmation alerts across all 15 process steps to align the efforts of more than seven various stakeholder entities,” adds Savoy-Burke.
Further, PFSCM’s process mapping revealed that several changes were made to the standard importation process.
Below are some examples of processes that have been amended:
- Preparation and follow up of duty waiver exemptions documentation.
- Submission of mandatory documents for customs clearance.
- Lodging customs entries or declarations to proceed with importation processes.
- Applying for wharfage charges.
- Physical verification of containers.
- Securing release orders from Tanzania customs.
- Getting port charges from the ports.
- Securing loading permits.
With accurate information in hand, PFSCM was able to report the facts to its stakeholders, and those involved in the importation process.
“PFSCM not only investigated and mapped the process for our own benefit, but also shared our findings with clients, peers and stakeholders, and advocated widely for the implementation of standardized processes that will benefit all,” explains Savoy-Burke.
PFSCM provided practical advice that is in line with best supply chain practices, to help the involved parties establish, document and implement the new processes to improve efficiency. Savoy-Burke, notes that PFSCM’s operational work organically turned into technical assistance as its private sector 3PL partners, and their in-country agents, assisted in equipping the government agency with tools and practical examples to execute complicated processes.
“Our 3PL partners, along with their clearing agents, demonstrated their immense experience and expertise by helping the newly appointed government agency to understand and organize their processes to better align with that of the parties involved in clearing and forwarding,” adds Savoy-Burke.
After remapping the importation process, PFSCM has been able to recover its service delivery performance.
Meanwhile, PFSCM’s importation process mapping capabilities have proven to be a valuable tool for other stakeholders as they plan their importation activities into Africa. The initiative has caught the attention of other trade experts, who are also advocating for inter-agency discussions, and a waiver and importation information clearinghouse for the sector.
In conclusion, Savoy-Burke reiterates the need for increased in-country stakeholder engagement. He emphasizes that those involved in clearing and forwarding need to understand the end-to-end process to ensure full endorsement, agreement and the successful transfer of ownership between processes.
“PFSCM is committed to strengthening supply chains through knowledge transfer, upliftment, education, and the implementation of best practices whether for supply chain, procurement or distribution.
“Working towards the common goal of better health outcomes for all, has always been a motivating force for PFSCM, and in the ever-changing public health space, it is crucial that stakeholders come together to solve shared problems for the greater good,” stresses Savoy-Burke.