In public health supply chain management, the goal is to get the right quantity, of the right products, to the right place at the right time, for the right price, and repeating this process to prevent stockouts.
But what happens with the waste created when the products have done their job? What do countries do with expired products? And how is hazardous waste moved and disposed of?
Background
According to World Health Organization (WHO) almost 80% of the waste generated by health care activities is comparable to domestic waste. The remaining 20% are considered hazardous materials that may be infectious, toxic or radioactive, and related risks have so far been only poorly investigated.[i]
In 2002, the results of a WHO assessment conducted in 22 developing countries showed that the proportion of health care facilities that do not use proper waste disposal methods ranges from 18 to 64%.[ii]
A lack of awareness about the health hazards related to health care waste, inadequate training in proper waste management, absence of waste management and disposal systems, insufficient financial and human resources and the low priority given to the topic are the most common problems connected with health care waste. Many countries either do not have appropriate regulations, or do not enforce them, reports WHO.[iii]
In response to this problem, WHO advocates for robust national action plans and policies for safe management of waste from health care activities and the implementation of the Libreville Declaration on Health and Environment in Africa.[iv] In 2008, ministers from 52 African countries committed to improving their health care waste management (HCWM) efforts under the guidelines and recommendations of the Libreville Declaration.
Through the support of WHO and other organizations such as GAVI and UNICEF, countries have been able to establish and improve health care waste treatment and disposal infrastructure, acquire the basic equipment such as color-coded bins, and train waste handlers.
To help countries strengthen their HCWM system the WHO provides guidelines for the management of health care waste in their comprehensive guidance document, Safe management of wastes from health-care activities.
Activities at the start of the supply chain that can reduce waste
As a specialized health care procurement services agent, the Partnership for Supply Chain Management (PFSCM) has experienced firsthand the complexities associated with health care waste reduction and management.
Not all health care waste can be prevented, but from a supply chain perspective, waste generated as a result of expired products, damages during transportation, unwanted donations (for example, those that do not meet country requirements or donations with low remaining shelf-life), counterfeit products, or unsuitable products (such as those with incorrect or untranslated labelling), can be minimized.
PFSCM 4PL Services Director, Ishmael Muchemenyi, explains that accurate forecasting and quantification, best procurement practices, well executed logistics, and proper inventory and warehousing management can significantly reduce the amount of heath care waste.
“The supply chain plays a critical role in reducing waste. PFSCM’s work starts at the very beginning of the chain; already here we have the ability to collaborate with recipient countries to ensure the right amount of the right products are being purchased, for the right purpose, at the right time.”
PFSCM has the responsibility to ensure that products arriving in-country have the highest probability of being consumed. This entails proactive engagement with country recipients to ensure the products are of the correct specification, with adequate shelf life, and that sufficient storage is available.
“We work closely with country recipients to ensure that products ordered are completely understood and fit for purpose. This comprises checking every detail such as labelling language, packaging specifications, county specific requirements and regulations,” notes Muchemenyi.
Apart from collaborating with country recipients, PFSCM also upholds a strict product quality assurance (QA) policy, which prevents costly and wasteful product recalls.
PFSCM only procures products that comply with defined quality requirements as prescribed in applicable QA policies, such as those that are either WHO prequalified, approved by stringent regulatory authorities or International Medical Device Regulatory Forum and meet national regulatory requirements. PFSCM adopts a risk-based approach to flag random products for sampling and quality control testing to ensure that the products continue to meet required specifications.
Further, Muchemenyi explains that working with reliable partners and embracing new technologies and innovations that provide end-to-end traceability, enables us to prevent counterfeit products from entering the supply chain, and quickly identify and eliminate falsified products should they be introduced.
In addition, to ensure product integrity during transportation, PFSCM’s 4PL Services division works with freight forwarding companies that comply with Good Distribution Practices. These freight forwarders employ advanced cold chain shipping, and temperature monitoring to help maintain product integrity during transportation.
“Any delays in the shipping and importation process reduces shelf life, and shipping products in unfit conditions, or failing to comply with stringent temperature control requirements contribute directly to waste,” adds Muchemenyi.
Overall, by employing best procurement and supply chain practices and maintaining good stakeholder relationships, organizations can reduce health care waste.
Reverse logistics of hazardous waste with limited resources, during times of conflict in Mozambique
Between 2014 and 2017, PFSCM, in collaboration with Fumigation International Mozambique, Enviroserv, and Imperial Health Sciences (IHS), provided procurement, warehousing, distribution, and waste management services of Dichlorodiphenyltrichloroethane (DDT) for one of the Ministry of Health (MoH) of Mozambique’s Indoor Residual Spraying (IRS) campaigns for the prevention of malaria.
PFSCM and the partnering organizations were responsible for the treatment and disposal of DDT contaminated waste products that resulted from the IRS campaign, which ran from the last quarter of 2014 to the first quarter of 2016.
At the end of the spraying campaign, all unused DDT as well as any dry waste and contaminated waste material such as the pouches that contained the DDT, had to be transported to an accredited waste disposal facility in Hamburg, Germany.
In total, 72.5 metric tons of DDT needed for the campaign entered Mozambique at the ports of Beira and Maputo in 2014. The products were warehoused at the two locations for repacking and then trucked to 11 districts across the country. Not only was the initial product distribution and warehousing a massive effort, but the waste collection and disposal that followed on completion of the spraying campaign also proved to be extremely challenging.
Before the waste products could be exported to Germany, they had to be collected from the 11 districts and consolidated at a suitable facility in Mozambique where they were repackaged, labelled and stored, while awaiting the Basel permit required to move the consignment.
Security threats, limited resource, the hazardous nature of the product, and the remoteness of locations made the handling, transport and collection, and storage of the DDT especially complicated.
Handling
DDT requires special care and handling in accordance with the Basel and Stockholm Conventions, and WHO and UN guidelines. The project team developed a set of Standard Operating Procedures, which was used to train, and guide staff in the safe handling of the waste. All waste handlers were also required to use the necessary Personal Protective Equipment.
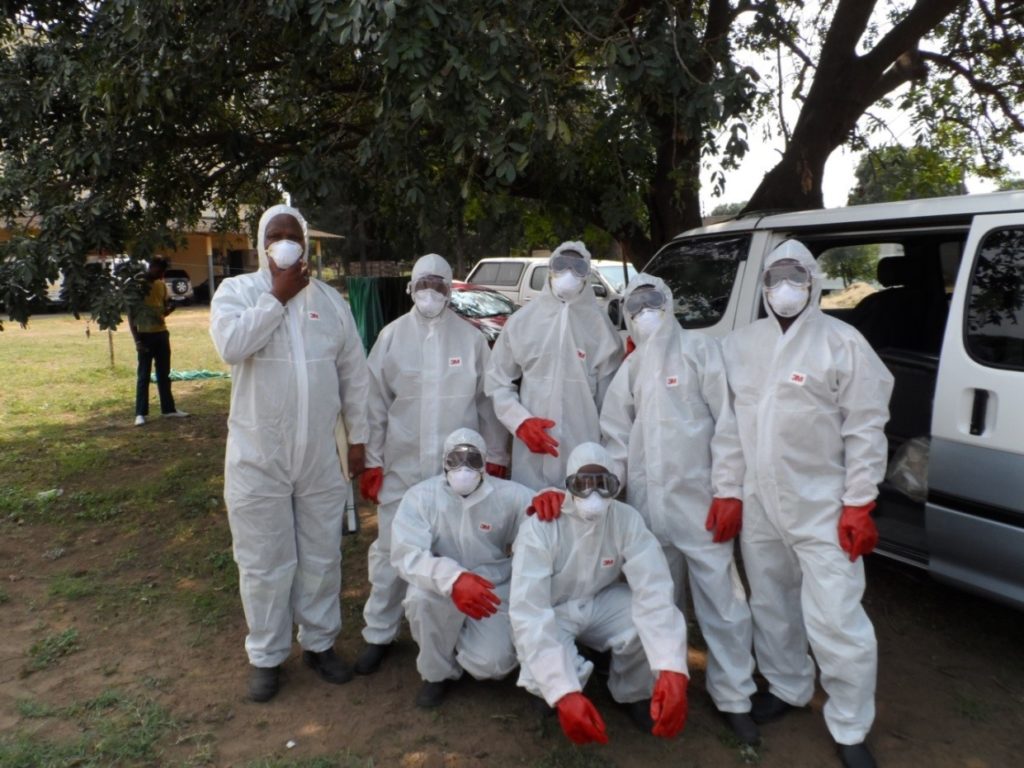
The Enviroserv team geared in full Personal Protective Equipment for waste handling.
Transport and collection
In 2016, unrest in the Northern territories of Mozambique resulted in targeted attacks on some of the routes that connect the North to the South. The security unrest halted the collection efforts. Alternative, non-road transport was investigated, but all options had major shortcomings.
During that time the Government of Mozambique deployed the military to manage the conflict areas and introduced strict travelling arrangements along certain routes in the central territories. Dedicated travel times with military convoys were instituted, and by October 2016, the security situation along the routes started improving.
The MoH commissioned three military convoys to accompany the waste collection vehicles, and by mid December 2016 all waste from the 11 districts was recovered.
Storage
While awaiting the Basel permit needed for transboundary movement of hazardous goods, the waste products were stored at the Mavoco waste site in Maputo for about a year. This is the only waste storage site in the area that is registered with the relevant authorities, and allowed to keep dangerous waste.
To ensure the safety and proper segregation of the waste at all times, it was stored in five lockable 20-foot storage containers.
The storage site had limited resources, and lacked weighing and handling equipment such as container cranes and gantry cranes; and it was also only partially paved limiting the movement of forklifts.
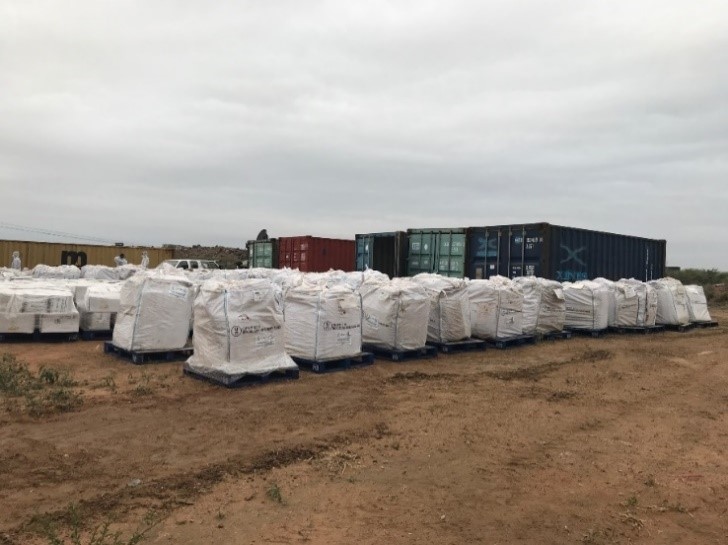
Palletized bags containing dry waste materials ready for loading into the containers destined for Germany.
Preparing for export (reverse logistics)
The disposal facility in Germany required the waste to be palletized for handling purposes. Mock packaging exercises were done to determine the optimal pallet configuration.
The procurement of the pallets had to be well-timed. The Mavoco site had no secure storage space to house the pallets, therefore the arrival of the pallets, the loading of the containers, keeping to the allowed parking time, and other administrative issues such as the expiry dates of the various permits had to be synchronized.
Products were repackaged to make sure the packaging material was durable enough to withstand the transport conditions from Mozambique to Germany. Many precautions were taken including: not stacking products more than three levels high, shrink wrapping products onto the pallets, and fitting the release handles of the drums containing DDT with extra locking mechanisms.
Due to the stringent labelling requirements for hazardous waste — and to avoid rejection of the consignment at any of the various inspection points during the export, transportation and importation — the project team consulted with the shipping agent, and the waste incineration service provider to decide on the exact placement, size, information and layout of the labelling to be attached to the product.
Lastly, all export documentation was prepared and, as the loads were prepackaged, palletized and pre-labeled, the loading took place as soon as the containers arrived at the Mavoco site.
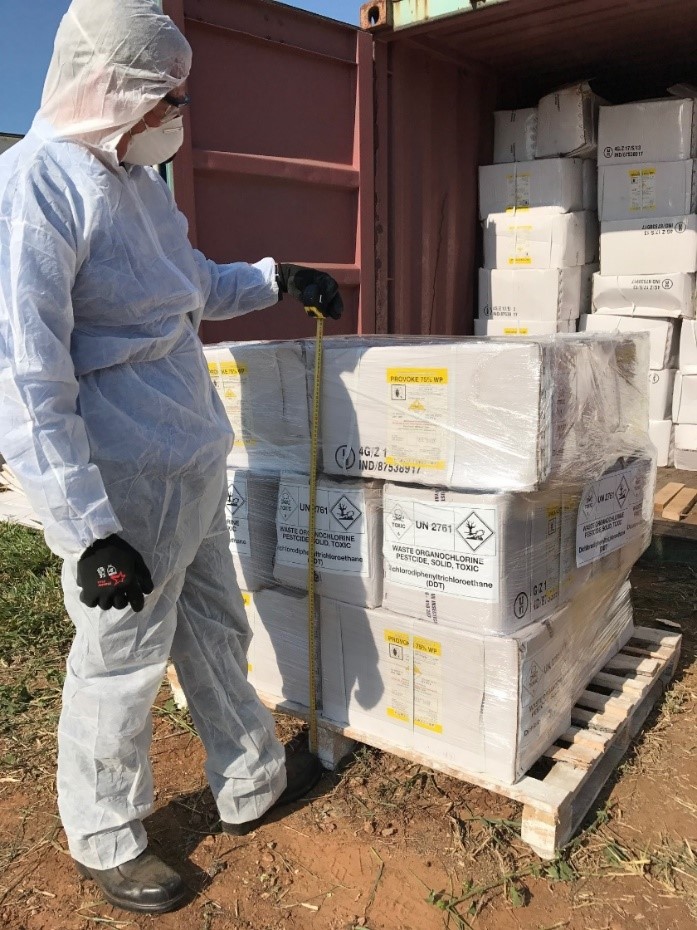
A mock packaging exercise undertaken with measurement of pallets in different configurations.
A long journey comes to an end
Finally, more than two years after the start of the spraying campaign, the DDT waste was ready to be exported.
In total, two 40-foot containers and one 20-foot container, containing about 15,000 kg of products, were shipped to Germany. The containers were trucked over a short distance of about 30 km from the Mavoco site to the Port of Maputo, where the consignment arrived well within the deadline for shipping.
Reflecting on the journey, PFSCM and its partners had to overcome five major challenges: the handling of dangerous goods, security threat on routes of collection, limited resources at the sole storage site, and a long wait time for the Basel export permit.
“When it is all said and done, dealing with waste management is a long and tedious process and one that poses significant risk if not professionally managed,” concludes Muchemenyi.
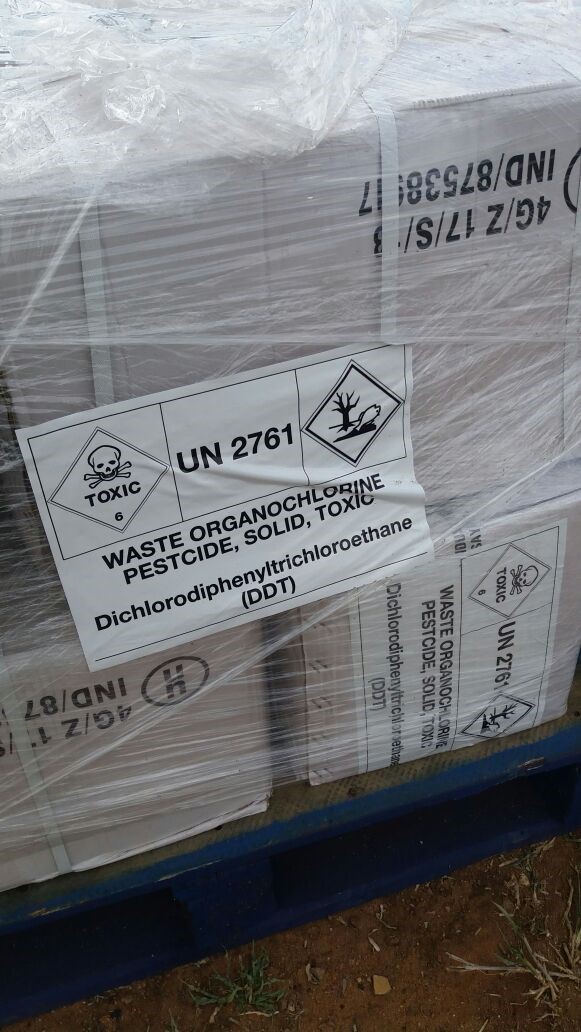
The labelling requirements were checked extensively to avoid rejection of the consignment at any of the various inspection points during the export transportation and importation.
Reference list:
[i] World Health Organization. “Advocating for national action plans for safe management of waste from health care facilities.” www.afro.who.int.
https://www.afro.who.int/sites/default/files/2017-06/PHE-Framework-for-health-care-waste-management.pdf (accessed October 1, 2019)
[ii] World Health Organization. “Safe health-care waste management: Policy Paper.” www.who.int
https://www.who.int/water_sanitation_health/facilities/waste/en/hcwmpolicye.pdf?ua=1 (accessed October 1, 2019)
[iii] World Health Organization. “Health Care Waste.” www.who.int
https://www.who.int/news-room/fact-sheets/detail/health-care-waste (accessed October 1, 2019)
[iv] World Health Organization. “Advocating for national action plans for safe management of waste from health care facilities.” www.afro.who.int.
https://www.afro.who.int/publications/advocating-national-action-plans-safe-management-waste-health-care-facilities (accessed October 1, 2019)